Competence, Skills and Capabilities Required for Smart Manufacturing in the Future
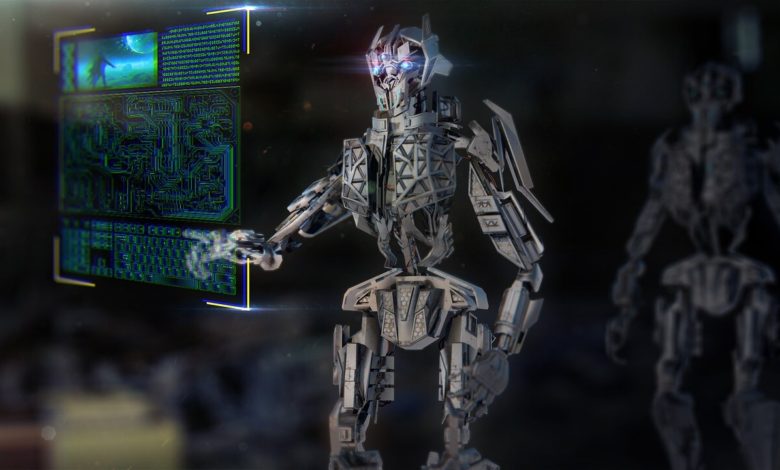
Smart Manufacturing and Industry 4.0 are characterized by small, decentralized, digitized production networks. In addition, it acts autonomously and can efficiently control its operations in response to changes in the environment and strategic goals. Companies in such a network are called Smart Factories or Intelligent Manufacturing (SF / SM).
This type of network is linked to a larger value chain network that has the responsibility to fulfill a specific customer demand. Additionally, assets such as machines and materials lie below the entire automation pyramid, but they are all well integrated through standardized interfaces. Finally, in the manufacturing process, machines and products can be inimitably defined and are always placed throughout their entire life cycle. These smart materials and products are tailor-made largely to mass production costs in the Smart Manufacturing and Industry 4.0 revolution.
Personal Competencies
What kinds of personal competencies, skills and abilities are required to fully comply with the Smart Manufacturing and Industry 4.0 revolution? Such competencies can be viewed as a person’s ability to act in a reflective and autonomous way. In summary, this type of competence includes the ability to learn (develop cognitive abilities), develop one’s own attitude and ethical value system that a person may have. Additionally, at a worker level, Intelligent Manufacturing and Industry 4.0 created an environment of increasing automation of routine tasks never witnessed before.
Today’s employees have to face the fact that their current job is no longer available in the future, because the future promises an uncertain business world. Workers’ tasks continue to change rapidly, and there is a need to continue changes in tasks. The rationale for this is that digital devices, Internet of Things and Networked Systems eliminate some or most of the tasks that the worker is currently performing. This may require the ability to look at one’s perspective of duty, taking into account the larger picture of society as a whole (difficulties, scarcity of resources, opportunities, and wealth).
In addition, opportunities for one’s own development and a commitment to lifelong learning should be the responsibility of both the individual and the organization. However, commitment to developing a naive technology rather than a critical attitude towards technological advances is a key asset for the future employee and organization in the Smart Manufacturing and Industry 4.0 revolution. Personal flexibility in terms of uptime, job contents, workplaces and mentalities are the prerequisite competencies for agile manufacturing to quickly respond to market needs and environmental conditions. In addition, as Smart Manufacturing and Industry 4.0 teams are diverse in terms of culture, education, and geographic location, today and tomorrow’s managers need the ability to transform their management and leadership styles from power-based to value-oriented.
Social (Interpersonal) Competencies
It is thought of as an individual embedded in a social environment, such as people and organizations, and also needs the ability and structures to communicate, collaborate and establish social connections with other individuals and groups. This is because of the social systems in which organizations interact between different actors (human-machines, human-human, etc.). The full digital integration and automation of Smart Manufacturing processes in vertical and horizontal dimensions also requires an automation of communication and collaboration mainly through standardized processes.
As a result, employees are responsible for a wider range of processes and need the ability to understand the relationships between processes, information flows, possible disturbances, and possible solutions to such interfaces. The increase in the scope and complexity of Smart Manufacturing and Industry 4.0 requires a mindset to build and maintain networks of experts who can collaborate to find ideal solutions to a particular problem. At present, Human work is now concentrated at the edges of interfaces where human flexibility and creativity in problem solving are strategic. Therefore, allowing creative activity in distributed social environments that include heterogeneous interdisciplinary and inter-organizational teams requires the ability to convey complex problems in different languages.
Therefore, today managers must create or act as agents that allow social processes not only within traditional organizational boundaries, but also mutual decision processes for the entire network. Social media plays a key role as supportive technology in the Smart Manufacturing and Industry 4.0 revolution. Managers, engineers and workers now have to demonstrate literacy, skills, knowledge and abilities with different technical communication and support systems tastes.
Competencies Related to Action
The competencies of an employee regarding action can be understood as the ‘ability to put individual or socially constructed ideas into action’, which makes dreams come true in the Smart Production and Industry 4.0 revolution. It is the ability of an individual to integrate concepts into his own agenda, successfully transforming plans into reality, not only at the individual but also at the organizational level. It should be noted that these concepts can be in summary forms and therefore should be reflected in their true meanings.
Digitization production inevitably leads to high financial and technological efforts for Smart Manufacturing and the Industry 4.0 revolution. The inherent risk associated with such efforts requires pragmatic thinkers and actors to bring the ‘too high’ vision of the Industry 4.0 revolution to the workshop where most workers are engaged. Both managers and employees need strong analytical skills and skills to find field-specific and applicable solutions without losing the overall goal of core competencies. Therefore, to achieve this, managers must break down complex concepts into realistic work packages, find and assign appropriate people and teams.
Smart Manufacturing and Industry 4.0 is not a simple methodology or technology. Managers need to encourage taking new routes and also take into account the risk of failure. For employees and managers, a strong interdisciplinary “out of the box” orientation can make it easier to find solutions in complex environments.
Competencies Related to the Field
This refers to the ability to access and use domain information for a job or a specific task. Key elements of domain knowledge are methodologies, languages, and tools designed for problem solving or business domains that reach beyond the marginal. One of the key elements of the Smart Manufacturing and Industry 4.0 revolution is the complete digitalization of planning and the use of data. Full digitization actions are in the form of smart planning, control production processes and networks. Production processes and networks (future ones) have domain-specific features that require domain-specific competencies. Digitized and intelligently managed production processes require studies that understand the basics of networking technologies and data processing. Therefore, workers need to assess whether subsystems are working as expected and be able to interact with such systems through appropriate interfaces. In case of disruption, workers and engineers should be able to analyze complex systems through special software.
Engineers are required to acquire skills, knowledge and abilities about cutting-edge software architectures, modeling and programming techniques. Additionally, statistical methods and data mining techniques are key skills for future production engineers. In summary, Smart Manufacturing and human-machine interfaces in the Industry 4.0 revolution should be developed based on a task and situation-oriented user-centered approach.